Underwater welding is a lucrative yet dangerous field and one of the best paid undertakings for commercial divers.
Since ships are subject to extraneous conditions like storms and ice or may become damaged by collisions and accidents, they sometimes require intervention by underwater welders.
Here’s a short intro for everything that you need to know about underwater welding.
What Is Underwater Welding?
Invented in the 1930’s, underwater welding is used for maintaining and repairing fully or partially submerged marine structures and vessels. Underwater welders are commercial divers that apply their trade on anything made of steel that happens to be subsea. This could be everything from ships, to structures, to oil and gas pipelines.
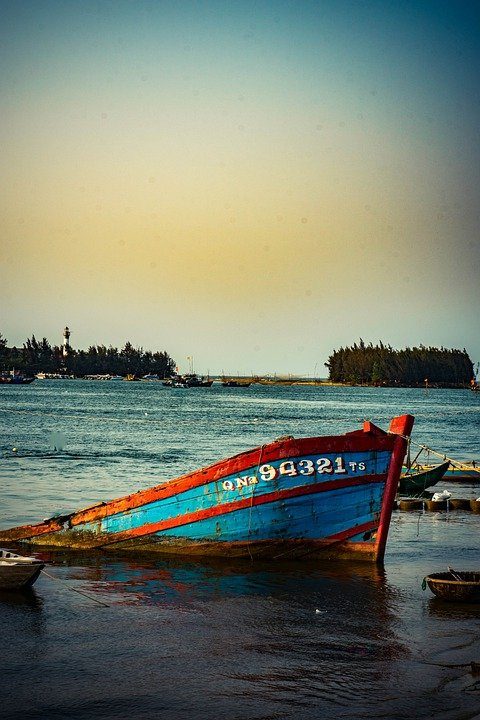
Types of Underwater Welding
Just as the name implies, underwater welding is the process of welding or ‘joining’ pieces of steel together underneath the water using electricity.
Here are the 2 most common underwater welding methods:
Hyperbaric Welding: Refers to dry welding techniques carried out in pressurized environments. Its application is limited to cofferdams or hyperbaric chambers, which are installed and de-watered over the desired work location. (Think two ends of a deepwater pipeline). The chamber would be large enough to house the diver/welding team and all their welding equipment. This method of welding attempts to create a near-identical work environment to that on the surface, allowing for high-quality welds to be executed. TIG (Tungsten Inert Gas) and MMA (Manual Metal Arc) welding processes are commonly used in hyperbaric welding procedures.
Wet Welding: Refers to the use of waterproof MMA electrodes under the water’s surface. Its application is the most common amongst the other methods. However, it requires the greatest amount of skill from the diver/welder. In this welding method, the diver strikes an arc between the electrode and workpiece, when the electrode is consumed, a gaseous bubble pocket is formed over the melted weld pool creating a protective shield, which allows the exchange of weld material to be made. Although results produced by wet welding can be less desirable due to the increased risk of cracking, with the correct procedures and training it is possible to produce very acceptable welds using this method. Wet welding is perfect for temporary or non-load bearing repairs such as patching and sealing.
Why Is It Important?
Underwater welding is an ideal solution in case of emergency situations. It’s a cheaper option than chopping the entire effected part, mending it on land, and reinstalling it, and it’s usually cheaper than bringing the structure to the surface entirely.
Although somewhat costly, underwater welding is generally quick, efficient, and easily deployable in almost any situation. With no time wasted in dry-docking, welders can easily perform the task on-site while the vessel remains in water.
If you’ve got a vessel that needs cleaning or repair, you’ve come to the right place. Thai Subsea Services provides the finest hull cleaning services in all of Thailand. We do complete underwater hull inspections, offer rope guard and grating clearing, underwater welding services, and much more. As one of the most trusted offshore commercial diving companies and hull cleaners, you can trust your ship with us!
Get in touch with us at +66 993459494 or email us at sales@thaisubsea.com for more info.